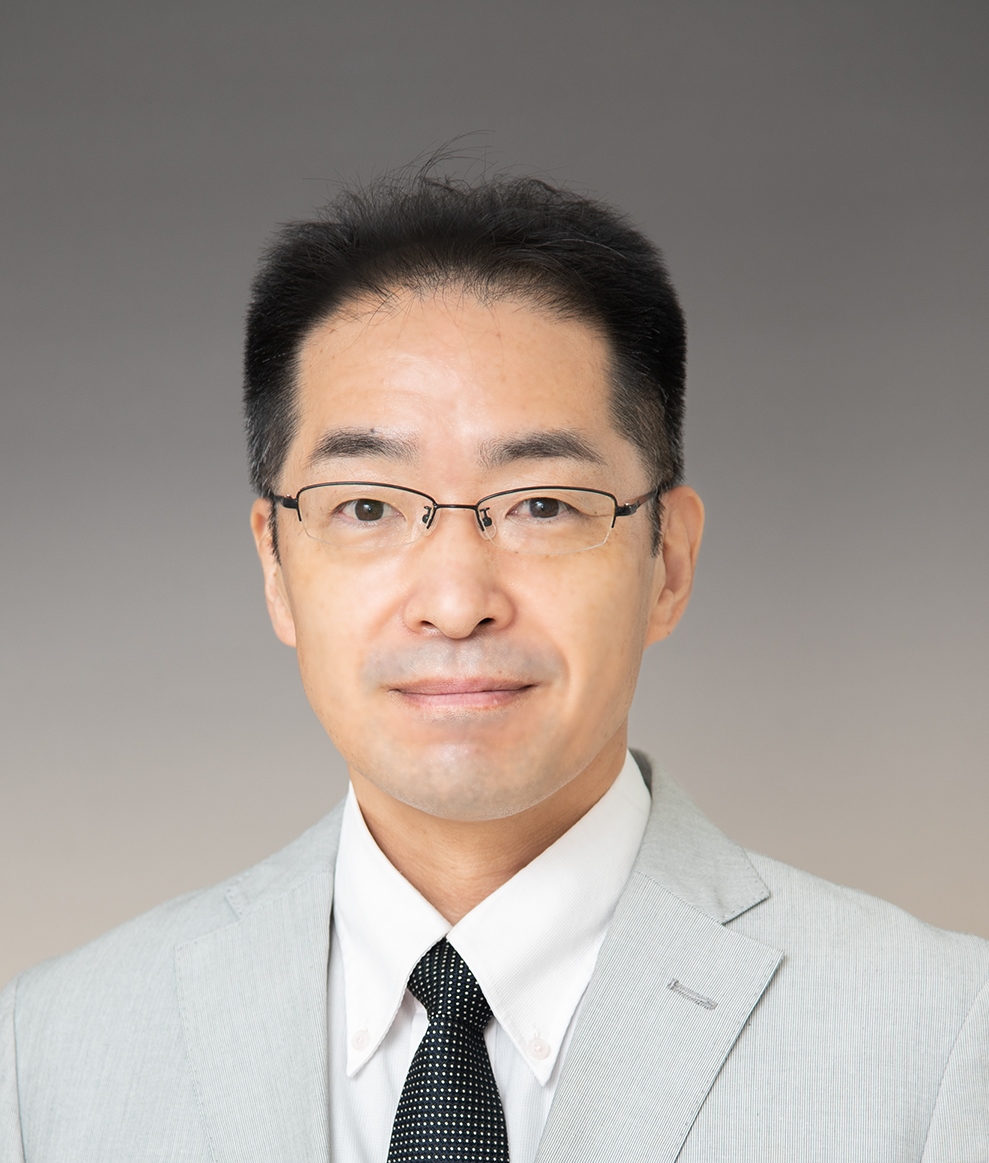
Prof.
Mikio Ito
Fukui University of Technology
|
Speech Title:
Fabrication
of Diamond Particle Dispersed Metal Matrix Composites by Spark Plasma
Sintering(SPS) for high thermal conductive materials
Abstract: Diamond-particle-dispersed-copper
(Cu) matrix composites were fabricated by spark plasma sintering (SPS)
process from the mixture of diamond particles and pure-Cu with addition
of a small amount of chromium (Cr) powder. The microstructures and the
thermal conductivities of the sintered composites were evaluated. These
powder mixtures were densely sintered by the SPS process at a
temperature of 1173 K for 600 sec. The relative density values of these
composites were found to be about 95%. Scanning electron microscopy and
X-ray diffraction analysis revealed that no reaction occurred at the
interface between the diamond particle and the Cu matrix phase under the
sintering conditions conducted in this work. The thermal conductivity of
the Cu/diamond composite was significantly improved by Cr addition. As a
result, the thermal conductivity of (Cu-Cr) -50 vol% diamond composites
reached 518-584 W/mK in a volume fraction range of Cr between 2.5 and
8.6 vol% in the Cu matrix. The trans granular fractures of diamond
particles were observed on the bending fracture surface of the
composites with Cr addition, indicating that the Cr plays crucial role
on enhancing bonding strength between diamond particles and Cu matrix
phase in the composites. It was also found that B addition was effective
for increasing thermal conductivity of Cu/diamond composites as well as
Cr addition.
Biography:
Prof. Mikio Ito received B.E., M.E, and Dr.E degrees from Osaka
University. He was an assistant professor and associate professor at
Osaka University, and is now a professor of Department of Mechanical
Engineering, Fukui University of Technology. His research interests
include development of novel powder metallurgy process, especially for
sintering process, and improvement of various
powder-metallurgy-processed functional materials, such as thermoelectric
and hard magnetic materials, etc.
|
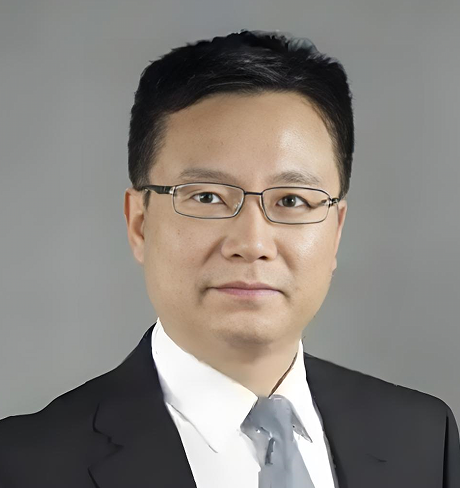
Prof.
Qingyuan Wang
Sichuan University |
Speech Title:
Very
High Cycle Fatigue in Additively Manufactured Alloys
Abstract:
As a new
industrial revolutionary manufacturing technology, additive
manufacturing (AM) plays a crucial role in the aerospace field. AM
technology is increasingly used in key equipment innovations, such as
advanced aeroengines (GE9X, GE) and aerospace engines (Raptor 3,
SpaceX). It is expected that with the maturity of AM technology, it will
be widely used in the future because of its significant advantages in
near-net forming etc. Due to inevitable AM defects, the need for
ultra-long-life durability of critical components in harsh service
environment is increasingly evident. Focusing on challenges of very high
cycle fatigue (VHCF) mechanics of AM aerospace alloys, this talk covers:
Ultrasonic fatigue testing with the loading frequency of about 20 kHz
was employed to research the VHCF
durability of typically AM structural metals for the aerospace, such as
the nickel-based superalloy (IN718 and IN939), titanium alloy (Ti6Al4V)
under elevated temperatures and various stress ratios, and aluminum
alloy (AlSi7Mg), which were fabricated by the laser powder bed fusion
(LPBF, one of AM technique). As a result, compared with those
conventional alloys, the AM alloys show lower fatigue strength. AM
defects (such as gas pore and lack of fusion), matrix (columnar grains),
and inclusions can act as initially fatal fatigue microcracks, and the
fatigue sensitivity level depends on the location, size, and type of
these defects. Defect-based modified fatigue life prediction formulas
were developed, which accurately predict fatigue life within a broad
life range. The fine granular area (FGA) region (one of the key
characteristic regions for VHCF) induced by grain refinement is composed
of many nanograins, which result from dislocation movement within
martensite laths. Dislocation pile-up and rearrangement in martensitic
laths form dislocation cells, which further develop into low-angle grain
boundaries and nanograins.
Biography: Qingyuan
WANG is a full Professor of Sichuan University since 2001. He was the
President of Chengdu University between 2014 and 2024. He received his
PhD in 1998 from Ecole Centrale Paris (University Paris-Saclay), France.
He has published over 300 papers (20 of ESI Hot Paper and Highly Cited
Paper) in SCI index journals, including Nature, Nature Commun,
Prog Mater Sci, Adv Mater, Adv Func Mater, Adv Science, Acta
Mater, IJ Fatigue, etc. He has chaired or co-chaired a
number of international or national conferences, including the 6th
International Conference on Very High Cycle Fatigue (VHCF-6, 2014),
2021+1 Chinese Congress on Mechanics, and the 55th of
Advanced Materials Congress (2023, Sweden), the 22th National
Conference of Fatigue&Fracture
(2024, Chengdu) etc. He has received a number of awards, including the
Distinguished Chinese Scholar Award from the NSF of China, The Second
Prize of National Natural Science Award, The First Prize of Sci & Tech
Progress (The
Chinese Society of Theoretical and Applied Mechanics),
Outstanding Paper Award of 2013-2023 (Materials Research Letters),
Senior Career Award of 2024 ( Inter J Structural Integrity),
ICCES Distinguished Fellow Award of 2024 and JSPS Fellowship Award of
2024. He is a member of European Academy of Sciences and Arts, European
Academy of Sciences and a Fellow of The Chinese Society of Theoretical
and Applied Mechanics.
|